Traditional Chinese Ceramic Techniques: Before Choosing Porcelain, Understand These 48 Professional Terms
Author: Yuan Taose Commune
Introduction
Traditional Chinese Ceramic Techniques blend cultural heritage with refined craftsmanship, carrying over a thousand years of legacy. Whether you’re an artist, a collector, or simply someone who appreciates the beauty of traditional handmade ceramics, learning these time-honored terms and methods helps you better understand their cultural significance. In this illustrated guide to 48 professional terms, we explore the core of traditional Chinese ceramic techniques—including shaping methods, decorative styles, and firing processes—that continue to inspire today’s ceramic artisans.
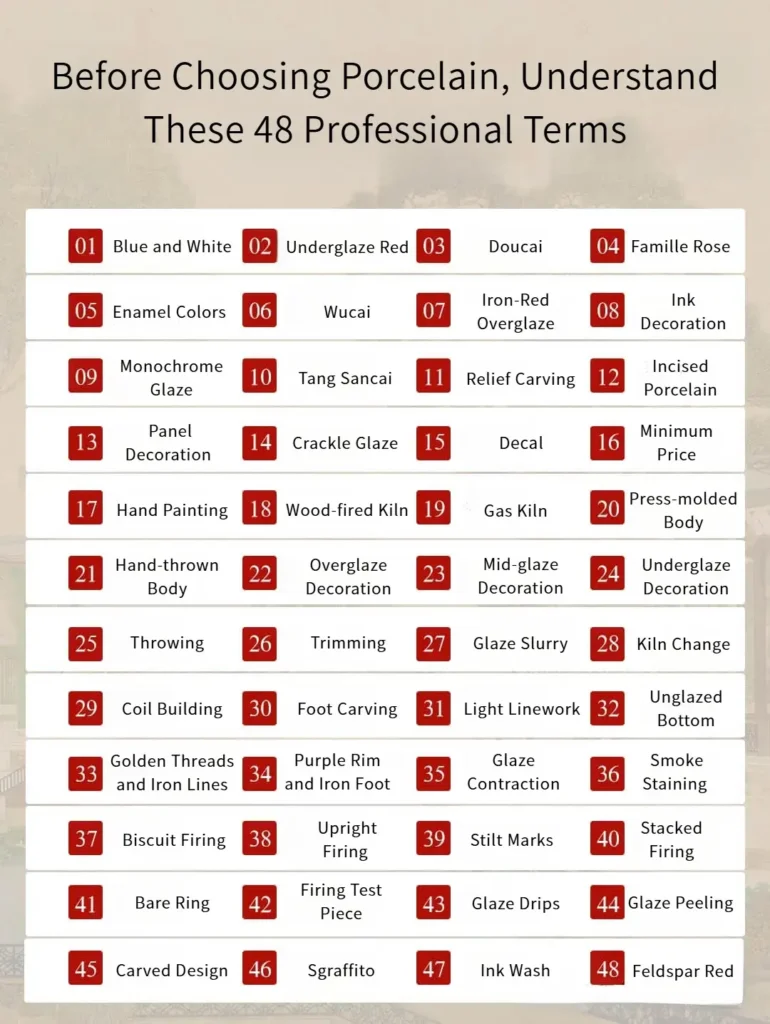
Handmade Ceramic Decorative Techniques
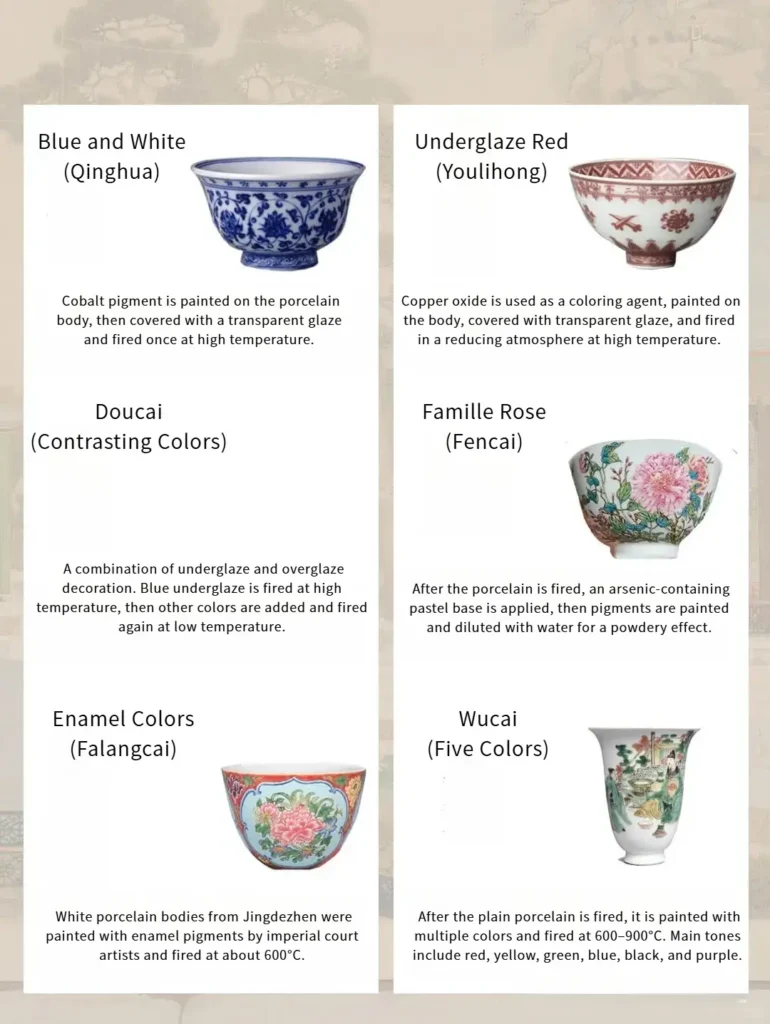
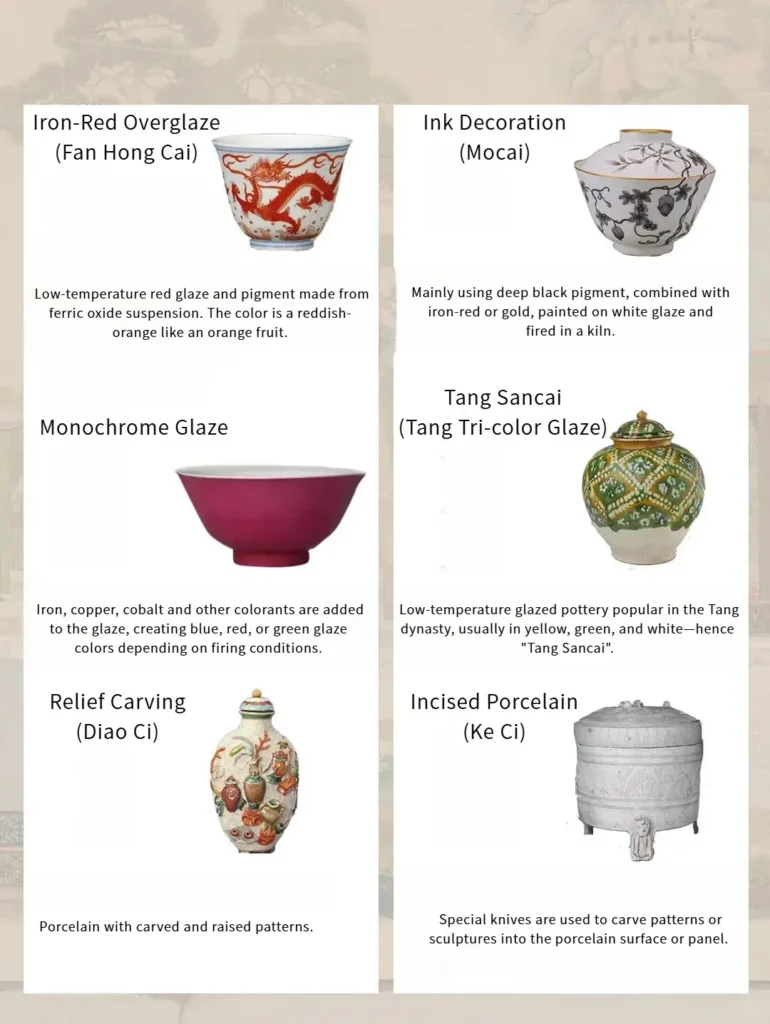
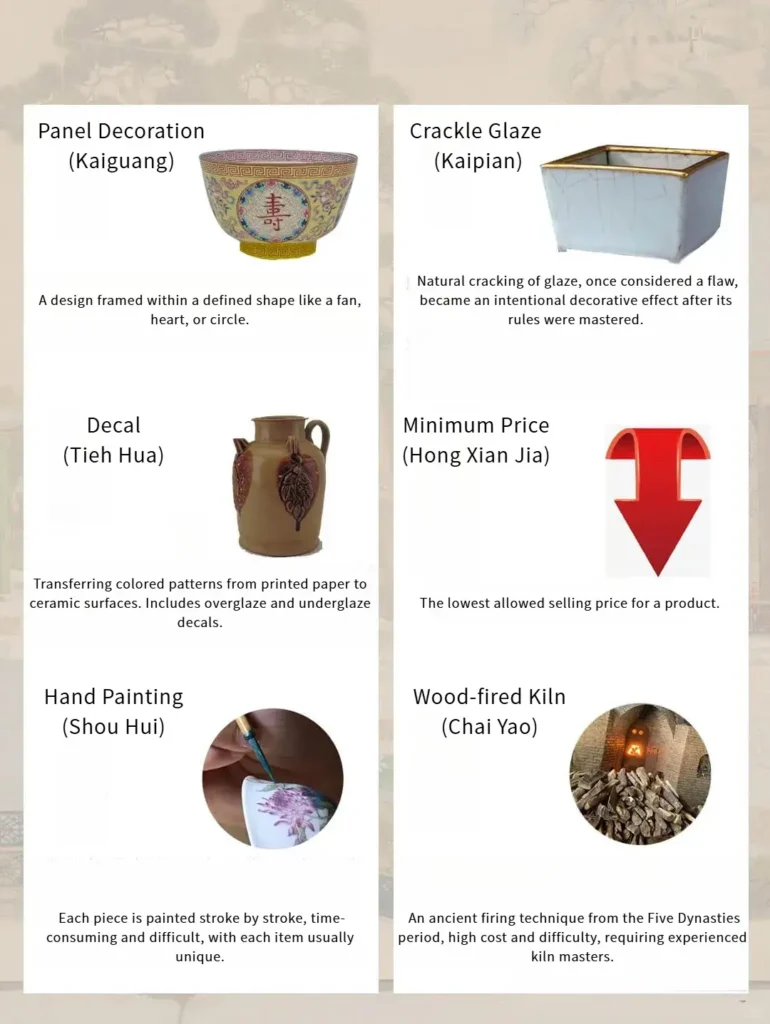
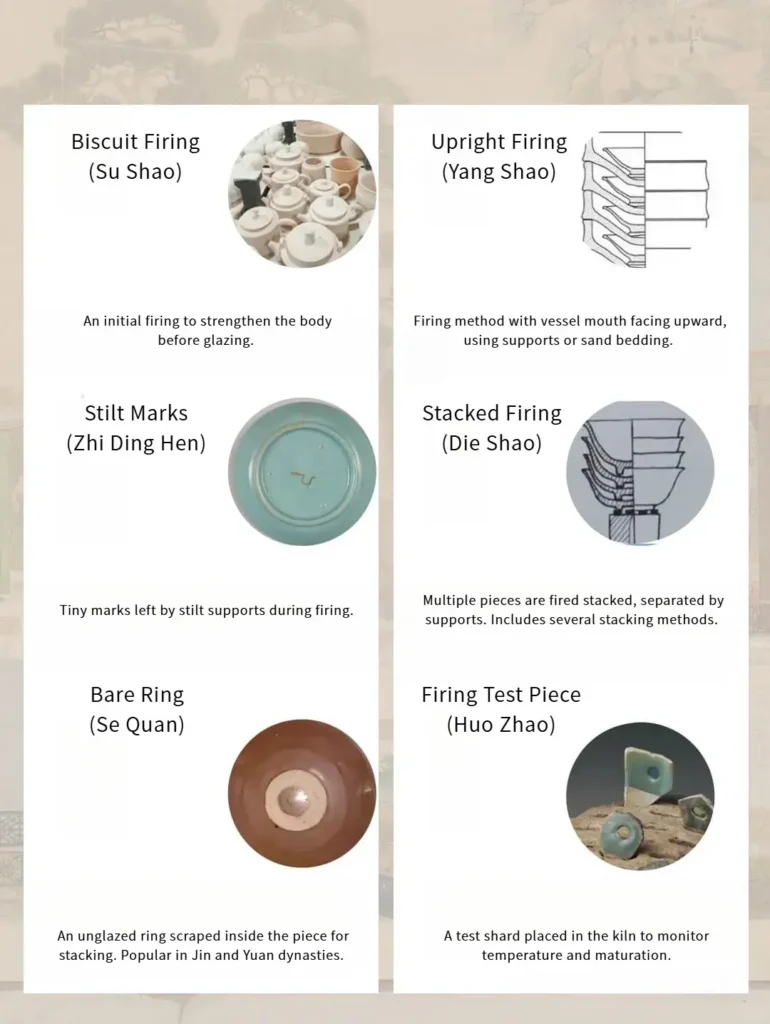
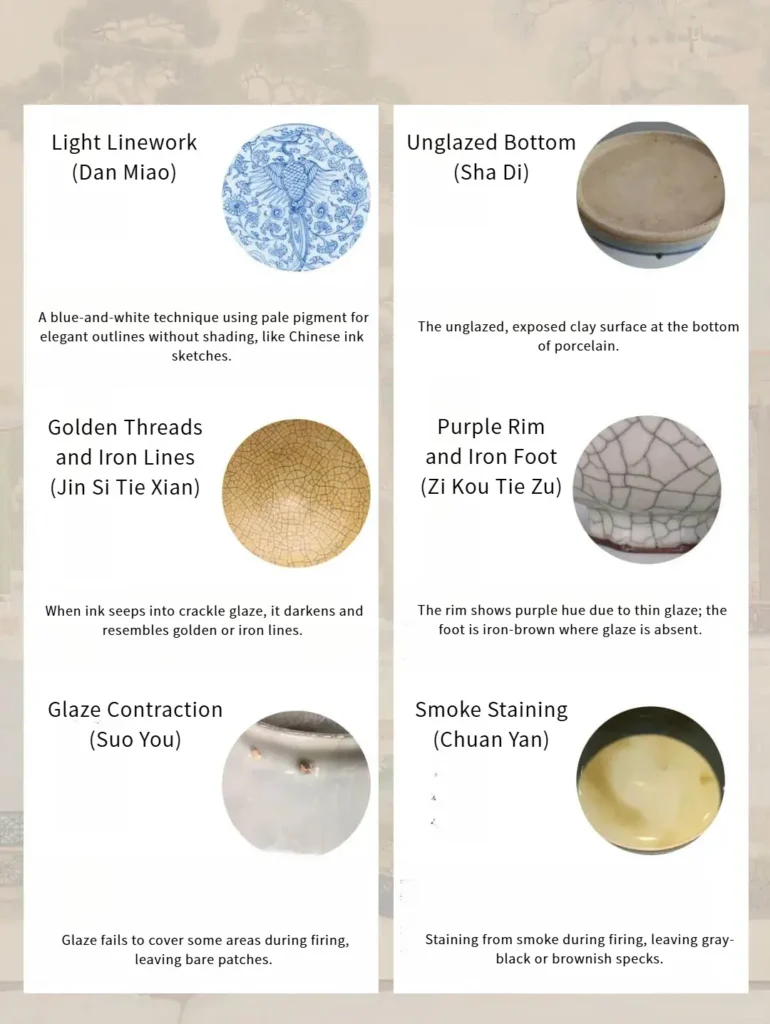
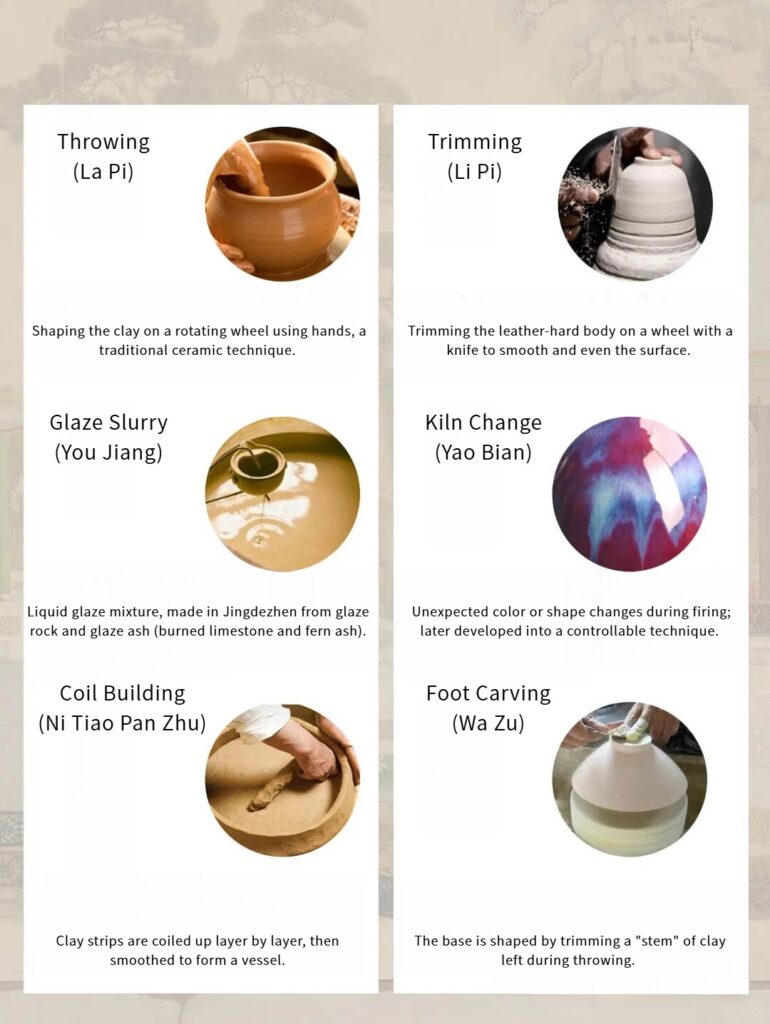
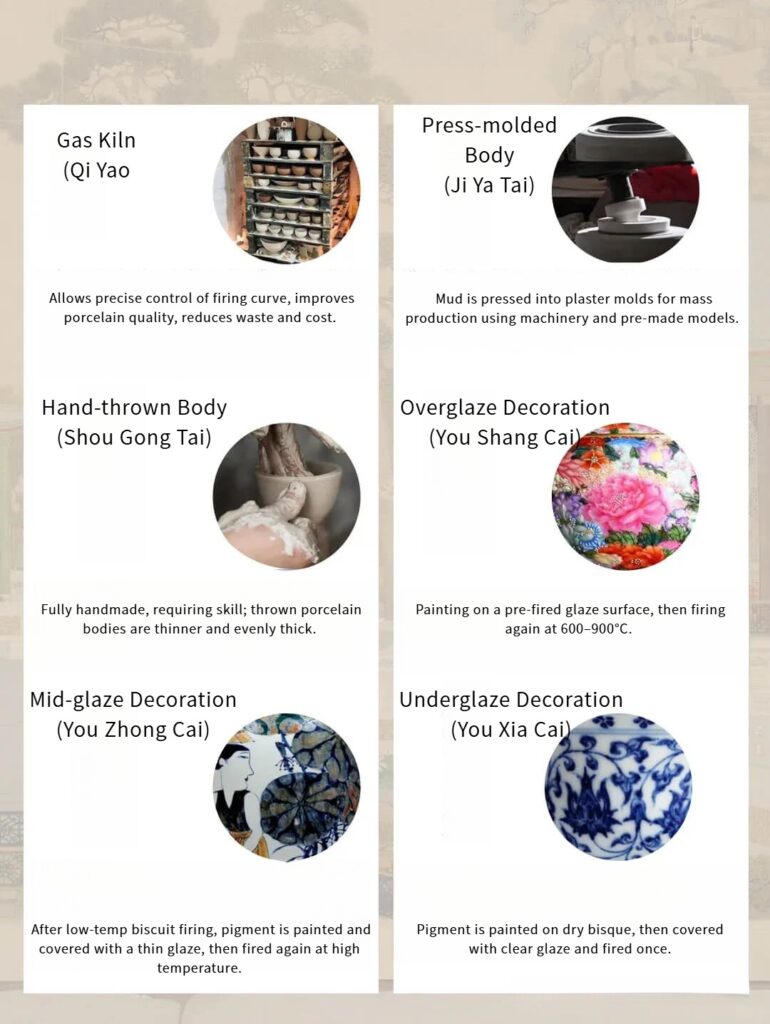
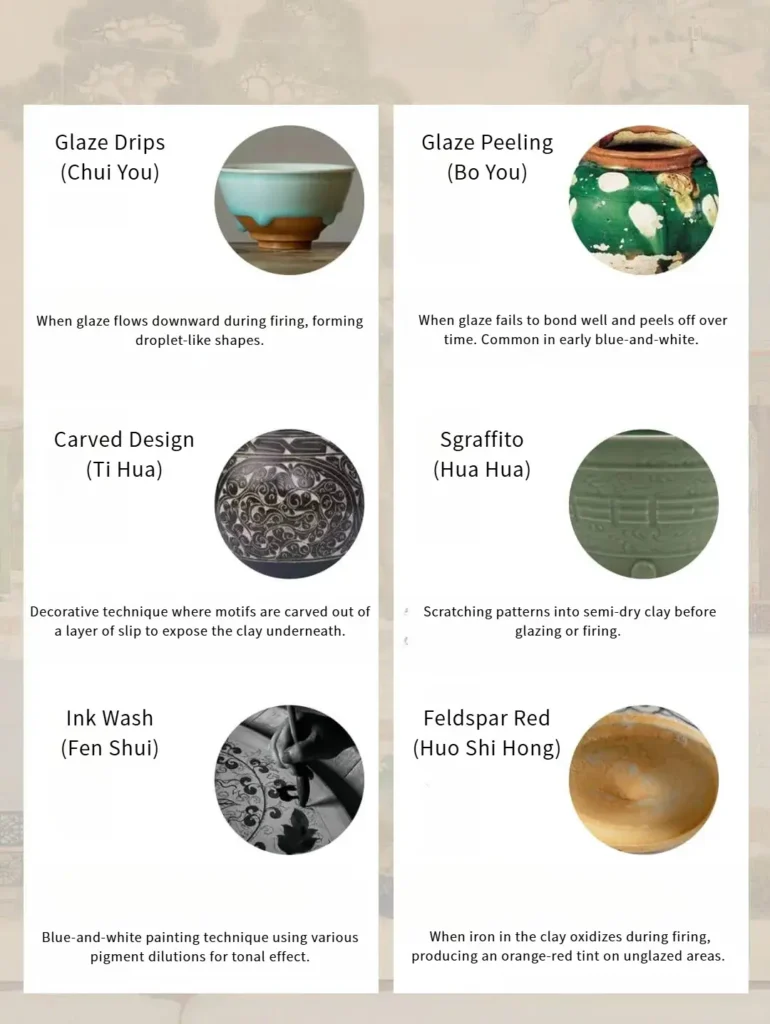
🎨 Color and Decoration Techniques
Blue and White (Qinghua)
Artisans paint cobalt pigment onto the porcelain body, apply a transparent glaze over it, and then fire the piece once at high temperature.
Underglaze Red (Youlihong)
Artisans use copper oxide as a coloring agent, paint it onto the body, apply a transparent glaze, and fire the piece in a reducing atmosphere at high temperature.
Doucai (Contrasting Colors)Artisans first fire the blue underglaze at high temperature, then apply other colors and fire the piece again at a lower temperature.
A combination of underglaze and overglaze decoration. Artisans first fire the blue underglaze at high temperature, then apply other colors and fire the piece again at a lower temperature.
Famille Rose (Fencai)
Artisans fire the porcelain first, then apply an arsenic-containing pastel base. After that, they paint pigments and dilute them with water to create a powdery effect.
Enamel Colors (Falangcai)
Imperial court artists painted enamel pigments onto white porcelain bodies from Jingdezhen and fired them at about 600°C.
Wucai (Five Colors)
After firing the plain porcelain, artisans paint it with multiple colors. Then, they fire it again at 600–900°C to fix the decoration.Main tones include red, yellow, green, blue, black, and purple.
Iron-Red Overglaze (Fan Hong Cai)
Low-temperature red glaze and pigment made from ferric oxide suspension. The color is a reddish-orange like an orange fruit.
Ink Decoration (Mocai)
Mainly using deep black pigment, combined with iron-red or gold, painted on white glaze and fired in a kiln.
Monochrome Glaze
Artisans add iron, copper, cobalt, and other colorants to the glaze, creating blue, red, or green colors depending on the firing conditions.
Tang Sancai (Tang Tri-color Glaze)
Low-temperature glazed pottery popular in the Tang dynasty, usually in yellow, green, and white—hence “Tang Sancai”.
🔧 Craftsmanship Techniques
Relief Carving (Diao Ci)
Porcelain with carved and raised patterns.
Incised Porcelain (Ke Ci)
Artisans use special knives to carefully carve patterns or sculptures into the surface or panel of the porcelain. This step adds intricate detail and artistic depth.
Panel Decoration (Kaiguang)
A design framed within a defined shape like a fan, heart, or circle.
Crackle Glaze (Kaipian)
At first, artisans saw natural glaze cracking as a flaw. However, once they mastered its patterns, they began to use it deliberately as a decorative effect.
Decal (Tieh Hua)
Transferring colored patterns from printed paper to ceramic surfaces. Includes overglaze and underglaze decals.
Hand Painting (Shou Hui)
Artisans paint each piece stroke by stroke. Because the process is time-consuming and technically demanding, each item is usually one of a kind.
🔥 Firing & Kiln Techniques
Wood-fired Kiln (Chai Yao)
An ancient firing technique from the Five Dynasties period, high cost and difficulty, requiring experienced kiln masters.
Gas Kiln (Qi Yao)
Allows precise control of firing curve, improves porcelain quality, reduces waste and cost.
Overglaze Decoration (You Shang Cai)
Painting on a pre-fired glaze surface, then firing again at 600–900°C.
Mid-glaze Decoration (You Zhong Cai)
Artisans first perform a low-temperature biscuit firing, then paint pigment, apply a thin glaze, and fire the piece again at high temperature.
Underglaze Decoration (You Xia Cai)
Artisans paint pigment on dry bisque, cover it with clear glaze, and fire it once.
Biscuit Firing (Su Shao)
An initial firing to strengthen the body before glazing.
Upright Firing (Yang Shao)
Firing method with vessel mouth facing upward, using supports or sand bedding.
Stacked Firing (Die Shao)
Artisans stack multiple pieces for firing and separate them using supports.Includes several stacking methods.
Firing Test Piece (Huo Zhao)
A test shard placed in the kiln to monitor temperature and maturation.
🧱 Body Forming Techniques
Press-molded Body (Ji Ya Tai)
Artisans press mud into plaster molds using machinery and pre-made models for mass production.
Hand-thrown Body (Shou Gong Tai)
Fully handmade, requiring skill; thrown porcelain bodies are thinner and evenly thick.
Throwing (La Pi)
Shaping the clay on a rotating wheel using hands, a traditional ceramic technique.
Trimming (Li Pi)
Trimming the leather-hard body on a wheel with a knife to smooth and even the surface.
Coil Building (Ni Tiao Pan Zhu)
Artisans coil clay strips layer by layer, then smooth them to form a vessel.
Foot Carving (Wa Zu)
Artisans shape the base by trimming a “stem” of clay left during throwing.
💠 Surface & Glaze Effects
Glaze Slurry (You Jiang)
Liquid glaze mixture, made in Jingdezhen from glaze rock and glaze ash (burned limestone and fern ash).
Kiln Change (Yao Bian)
Unexpected color or shape changes during firing; later developed into a controllable technique.
Glaze Drips (Chui You)
When glaze flows downward during firing, forming droplet-like shapes.
Glaze Peeling (Bo You)
When glaze fails to bond well and peels off over time. Common in early blue-and-white.
Light Linework (Dan Miao)
A blue-and-white technique using pale pigment for elegant outlines without shading, like Chinese ink sketches.
Golden Threads and Iron Lines (Jin Si Tie Xian)
When ink seeps into crackle glaze, it darkens and resembles golden or iron lines.
Purple Rim and Iron Foot (Zi Kou Tie Zu)
The rim shows purple hue due to thin glaze; the foot is iron-brown where glaze is absent.
Glaze Contraction (Suo You)
Glaze fails to cover some areas during firing, leaving bare patches.
Smoke Staining (Chuan Yan)
Staining from smoke during firing, leaving gray-black or brownish specks.
Bare Ring (Se Quan)
An unglazed ring scraped inside the piece for stacking. Popular in Jin and Yuan dynasties.
Stilt Marks (Zhi Ding Hen)
Tiny marks left by stilt supports during firing.
🖌️ Painting & Carving Techniques
Carved Design (Ti Hua)
Artisans carve motifs out of a layer of slip to expose the clay underneath, creating a decorative technique.
Sgraffito (Hua Hua)
Scratching patterns into semi-dry clay before glazing or firing.
Ink Wash (Fen Shui)
Blue-and-white painting technique using various pigment dilutions for tonal effect.
🧪 Material Phenomena
Feldspar Red (Huo Shi Hong)
When iron in the clay oxidizes during firing, producing an orange-red tint on unglazed areas.
💲 Market Term
Minimum Price (Hong Xian Jia)
The lowest allowed selling price for a product.