Glazing Methods and Related Notes for Porcelain- Under-glaze High-fire Jingdezhen Safe-glaze
This section introduces various glazing methods for porcelain, such as swing glazing for internal surfaces, blow glazing using special tools to apply glaze as mist, dipping glaze for trimming ware, and pouring glaze for large vessels; water replenishment is required before glazing, and inspection and repair are needed after glazing. It also mentions that colored glaze is applied by brushing or pressing, and that colored glazes may change during high-temperature firing, so perfect glaze formulas are necessary.
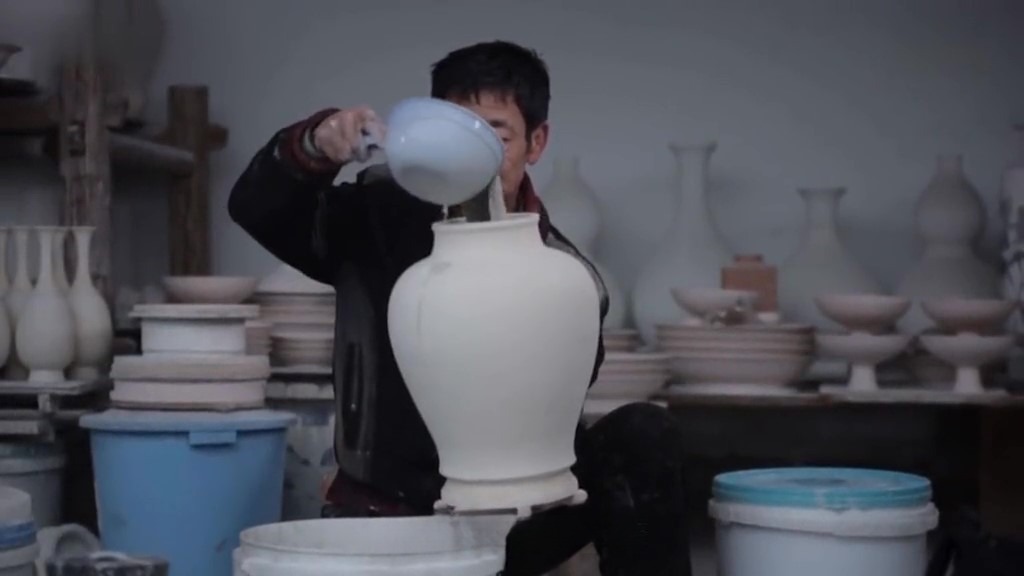
To apply glaze inside porcelain, the “swing” method is used. First, glaze water is ladled into the interior, then the piece is held by hand and gently swung so the glaze evenly covers the entire inner wall. The excess glaze is then poured out.
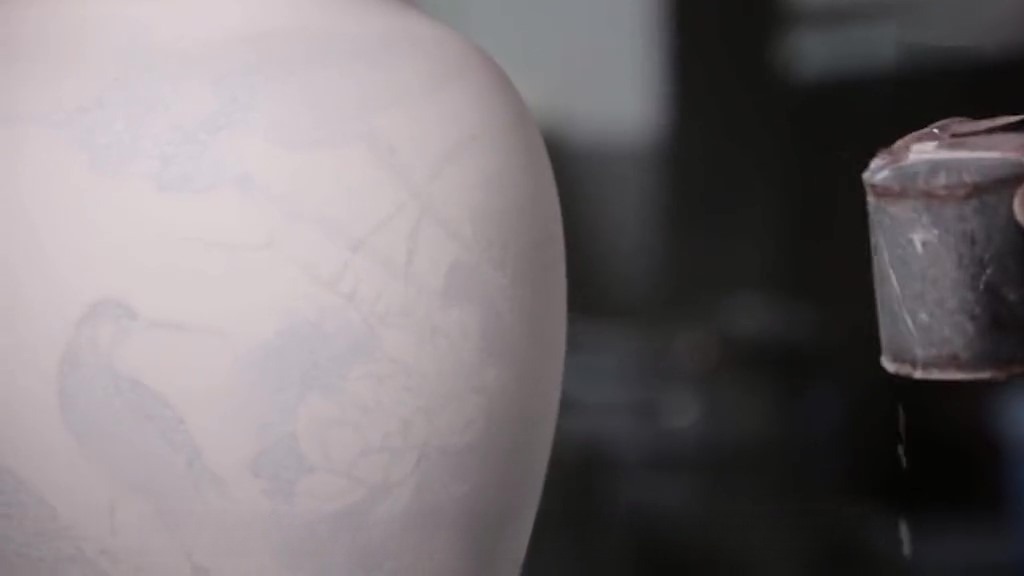
Blow glazing uses special tools. One end is covered with fine cloth, dipped into glaze slurry, and then air is blown from the other end so that the glaze attaches to the body in a mist form. The number of repetitions depends on the required glaze thickness; some pieces require up to seventeen or eighteen times.
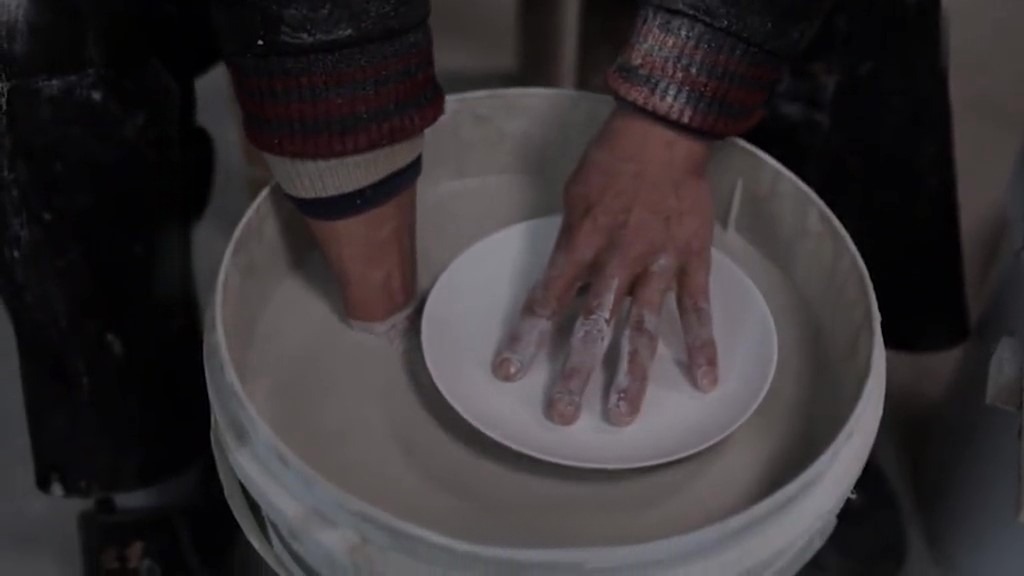
For the exterior glaze of small porcelain bodies, the dipping method is generally used. A hook is used to hold the base of the vessel, which is dipped into the glaze water. When the rim aligns with the glaze surface, it is immediately lifted—glazing completed in a single motion.
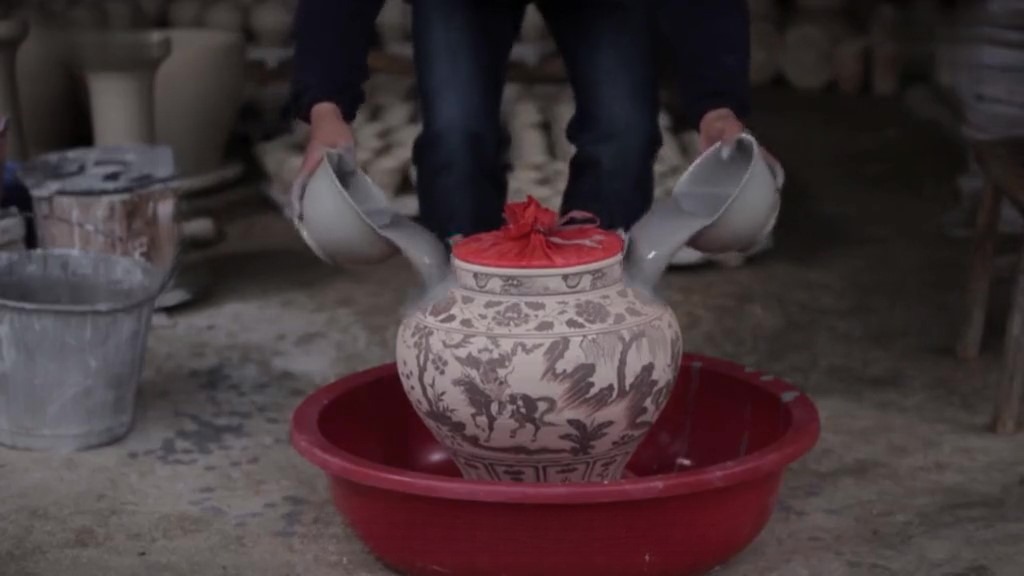
For large porcelain bodies, dipping or swinging cannot be used. Instead, the pouring method is applied. Each hand holds a bowl of glaze, pouring simultaneously from the left and right sides onto the center of the body—thus achieving complete glazing.
Before glazing, the porcelain body must be moistened. Using a water brush dipped in clean water to wipe the body can eliminate trimming marks and dust left from sun-drying. It also helps detect hidden air holes or hard clay lumps in the clay body.
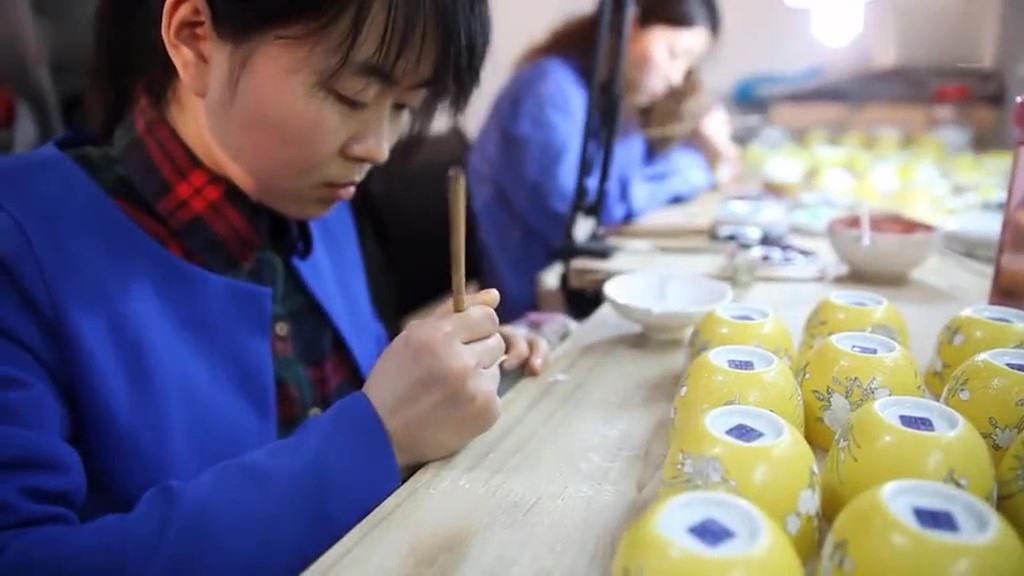
Repairs must be made promptly. After glazing, inspection is needed. Areas that lack glaze or where the glaze is too thin must be repaired using the same glazing method.
Because colored glaze slurry is relatively thick, it is only suitable for brushing or pressing onto the body using a brush. This method is called brushed glaze or pressed glaze. However, during high-temperature firing, a single colored glaze can result in several different colors due to various factors such as kiln temperature. Therefore, it is necessary to summarize experience and perfect glaze recipes.
Jingdezhen Porcelain Craftsmanship Introduction- Under-glaze High-fire Jingdezhen Safe-glaze
This section introduces various porcelain-making techniques, including “danmiao” outlining with cobalt blue, and “fen shui” shading within outlines; modeling techniques like pinching and carving; restoration of broken kiln furniture; and requirements for kiln loading. The full kiln process is the key to successful firing.
How can you tell the quality of porcelain painting techniques?
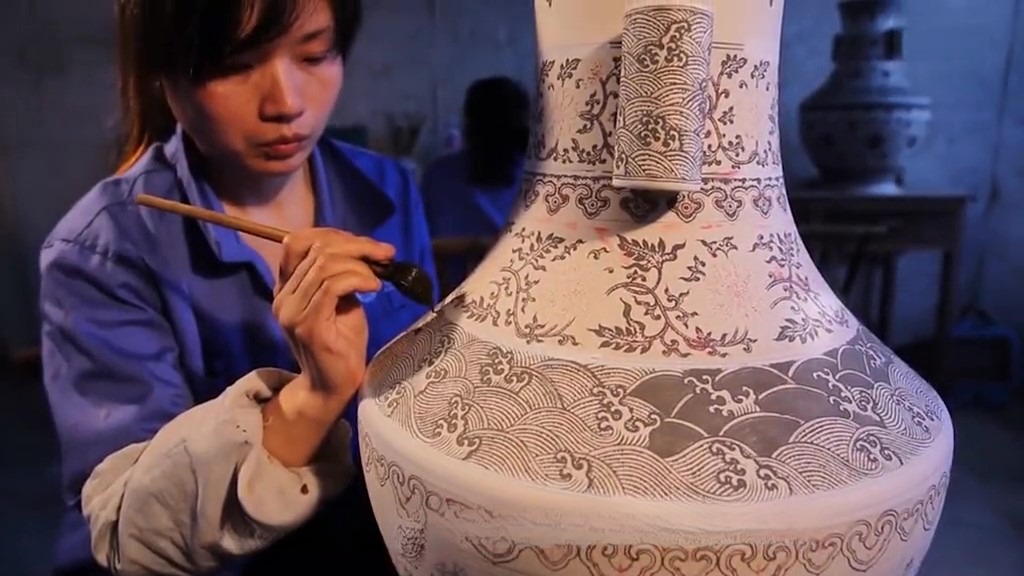
Using cobalt blue to outline pattern lines results in elegant and soft colors, resembling line drawings in Chinese painting. This type of blue-and-white painting is called danmiao. Fen shui (also called mixing water) involves filling in the outlined areas with cobalt pigment in varying intensities, creating the effect of “five tones of ink” seen in traditional ink painting.
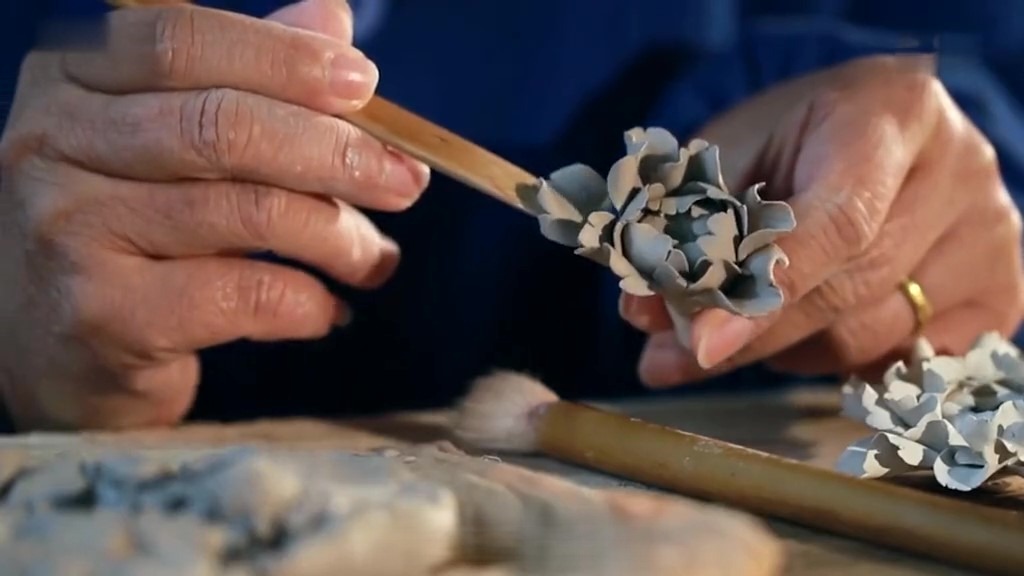
In porcelain sculpture, pinch modeling is used. A small amount of porcelain clay is placed in the palm, then shaped using pinching, trimming, carving, and pressing techniques to create lifelike birds and flowers. If a knife is used to carve directly onto the clay body, it becomes carved porcelain. These carved decorations are coated with transparent glaze and sent to the kiln for firing.

Pinch modeling includes many types. Most of the time, the details are made entirely by hand. For example, flower petals are usually pinched one by one. A chrysanthemum, for instance, is very difficult: each petal must be rolled into three or four tiny strips. The leaves are made broader. Different flowers and different artists produce different effects.
In ceramic sculpture, concise forms are used to express rich meanings. Unlike pieces that include poems or paintings as supplements, sculpture relies solely on form to speak—similar to how poetry conveys meaning through condensed language.
Why make a sheep this way? Do you like it or not? What color tone should be used? What does it express? That is for the viewer to imagine. Therefore, sculpture still needs further popularization at this stage.
What are the differences between traditional and modern porcelain firing methods?- Under-glaze High-fire Jingdezhen Safe-glaze
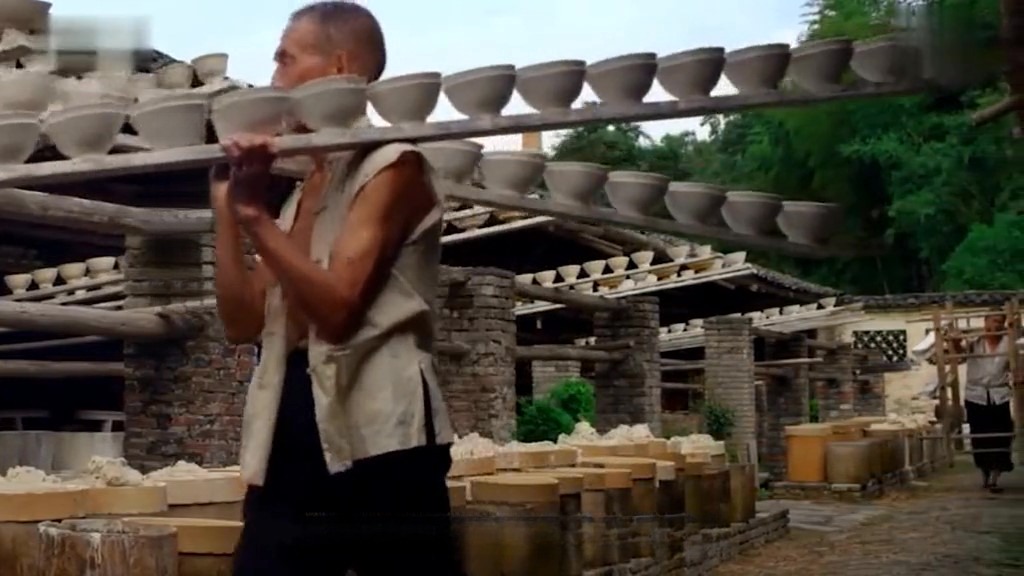
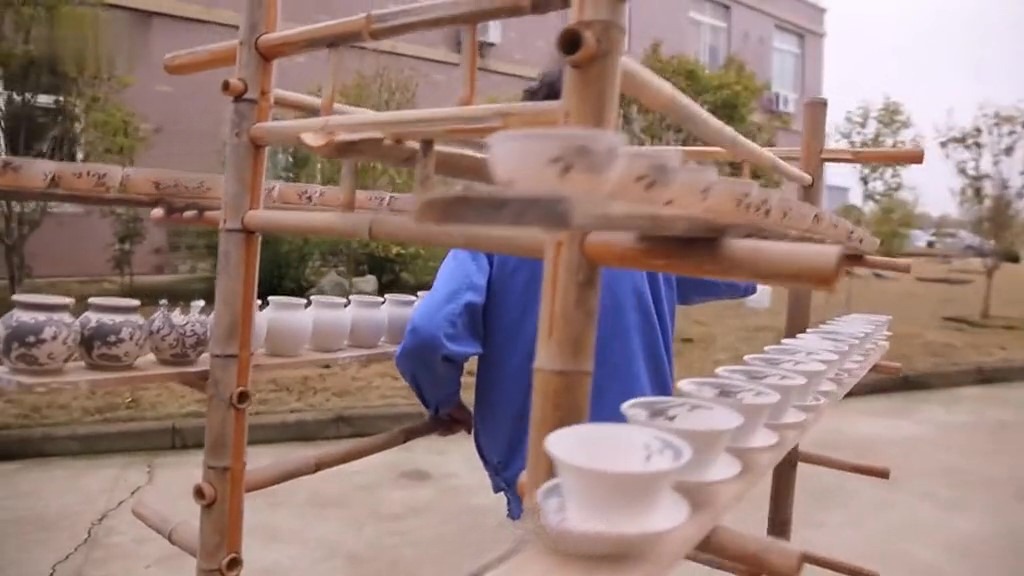
Porcelain bodies are transported from the forming workshop to the painting studio or kiln site by specialized workers. “Supporters” carry flat porcelain bricks on their shoulders, while “carriers” use bamboo racks with five tiers that hold over 100 pieces. Despite the load, they walk with steady steps, and the bodies do not sway—This is a unique spectacle characteristic of Jingdezhen
Kiln furniture like saggars become damaged after multiple high-temperature firings. Repairing them involves applying glaze water to the broken areas, then tightly tying them with bamboo strips or cloth. During firing, the saggar softens at high temperature, restoring the cracks.
When loading the kiln, the size and height of the porcelain bodies must match appropriate saggars. The saggars must be clean and placed level, without any tilting or shaking. Based on the glaze’s refractory properties and the porcelain’s requirements, the kiln master stacks the saggars by layering, standing, or vertical placement. The topmost saggar is called the “cap.”
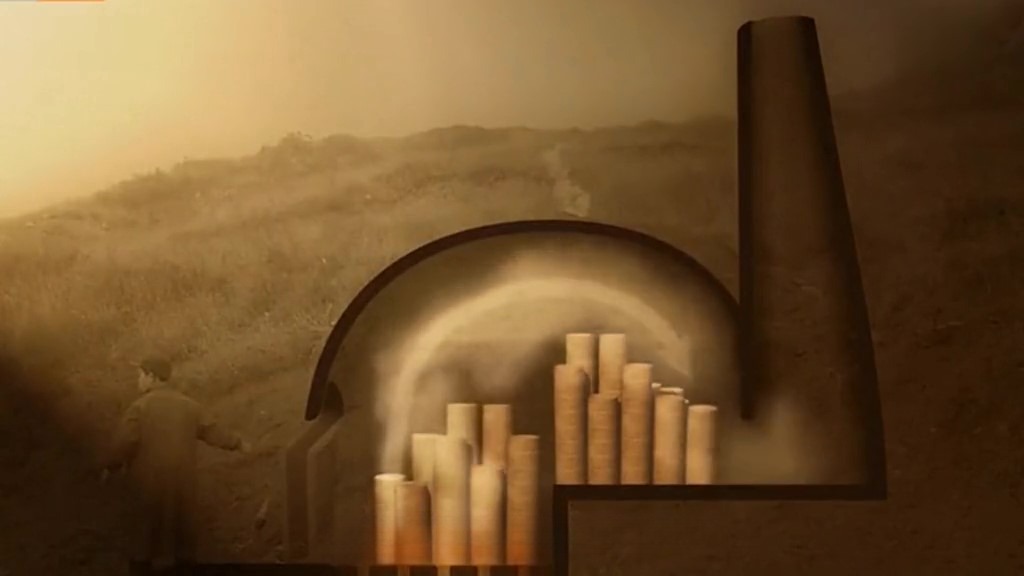
All the saggars in the kiln must be arranged in rows, straight and stable, with channels in between for flame circulation. This series of processes is called full kiln, and it is the most critical step in determining the success or failure of the firing.