This chapter introduces the Jingdezhen porcelain firing process. Pine wood is commonly used for firing kilns. During firing, workers continuously manage the wood and the kiln, responding to the instructions of the kiln master. After the fire is extinguished, kiln workers remove the porcelain pieces. If the kiln is damaged, an expert is needed for repairs. The porcelain pieces taken from the kiln are carefully inspected for quality, particularly the color. Porcelain pieces that require overglaze decoration must be paired or grouped accordingly. This chapter also explains the preparation of overglaze colors and the methods for sketching designs for porcelain painting.

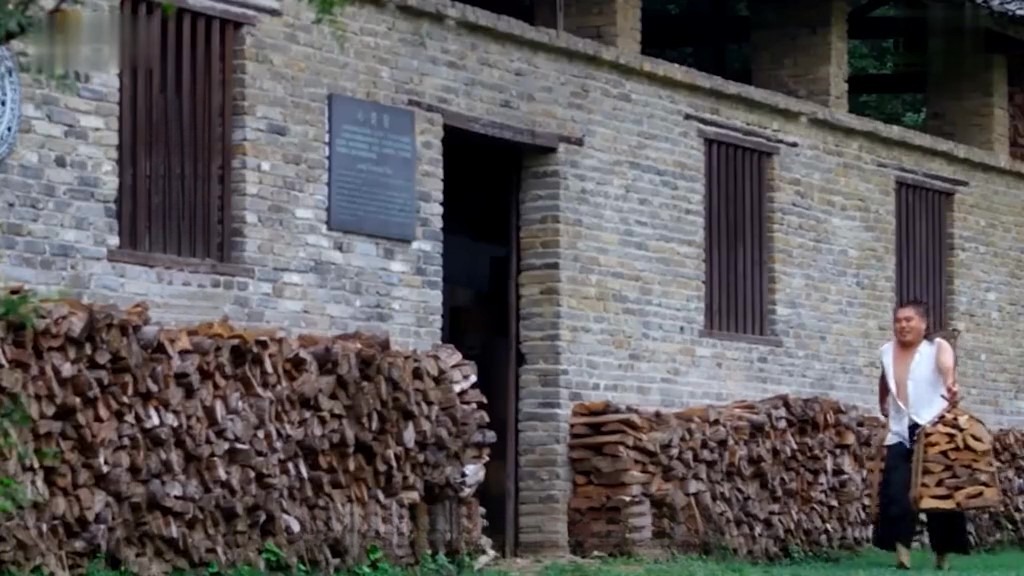
The firewood used for kiln firing is mainly pine wood because of its high resin content, which produces a long-lasting, stable flame. However, firing a kiln requires about 80-90 loads of wood. The workers involved in wood selection and kiln firing do not stop, and they follow the commands of the kiln master, who is in charge of controlling the heat.
When the firing stops and the kiln cools down, kiln workers enter the kiln to retrieve the porcelain pieces. After a rough selection, the pieces are placed in porcelain baskets and carried away.
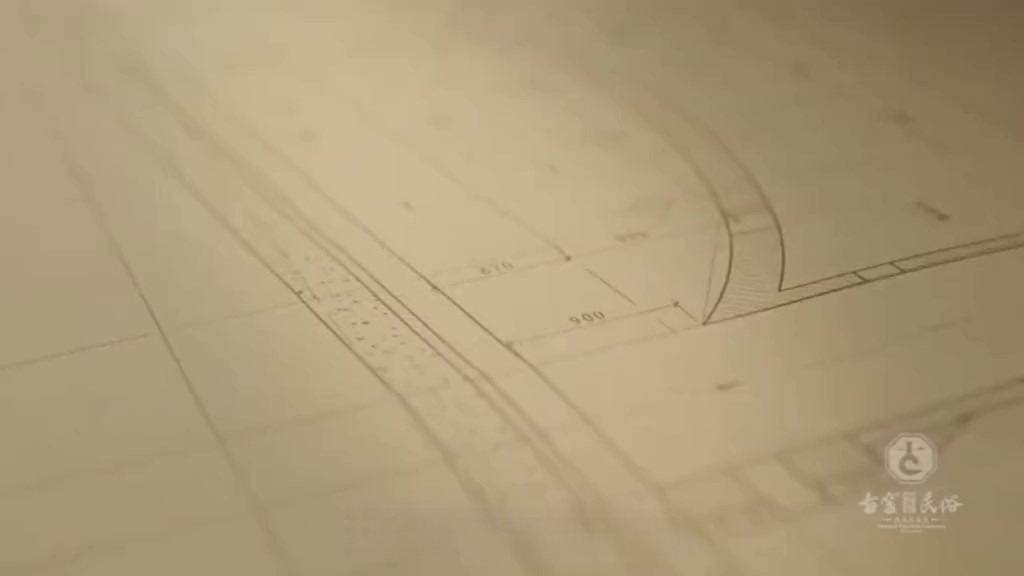
The quality and quantity of the firing are closely watched because pottery is the livelihood of the people, and there are significant economic implications. After several firings, the kiln may suffer damage, which requires an expert to repair it. They prepare a clay mixture with a syrup-like consistency, which is applied to the bricks to form a tight seal.
Porcelain pieces removed from the kiln need to be inspected for quality, a process known as “color inspection.” Additionally, porcelain pieces requiring overglaze decoration must be grouped or paired according to specific rules, such as matching vases or sets of tea ware and dinnerware.
Overglaze decoration involves painting various patterns on the glazed surface of already fired porcelain and then firing it again in the kiln. The colors are specially prepared by skilled workers, who grind and dry the pigments and then mix them in specific proportions, a process locally known as “color mixing.” With the development of the ceramics industry, traditional color mixing methods have gradually been lost.

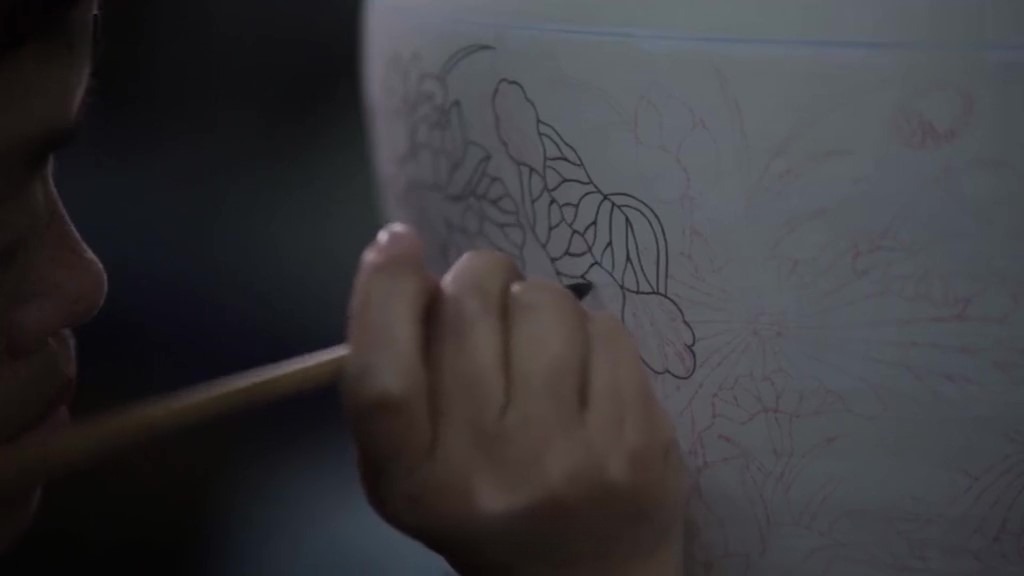
Decorative porcelain painting, whether of flowers, birds, or landscapes, requires attention to both form and spirit. Artists first create a draft, known as the “initial sketch,” which is approved by the client. Then, using an ink pen, they trace the design onto absorbent rice paper. After spraying it with water, the paper is placed over the porcelain and tapped with the palm, transferring the design outline onto the surface. This method ensures the painting is accurate and avoids significant errors.
This chapter focuses on the Jingdezhen porcelain firing process and the process of painting white glaze porcelain, including preparation work for pigments, painting according to the porcelain shape, and the fine division of labor in Jingdezhen.
It also discusses the difference between ceramic pigments and Chinese painting pigments, the process of firing decorations, red flower porcelain inspection, packaging, and transportation, and concludes with a tribute to traditional artisans.
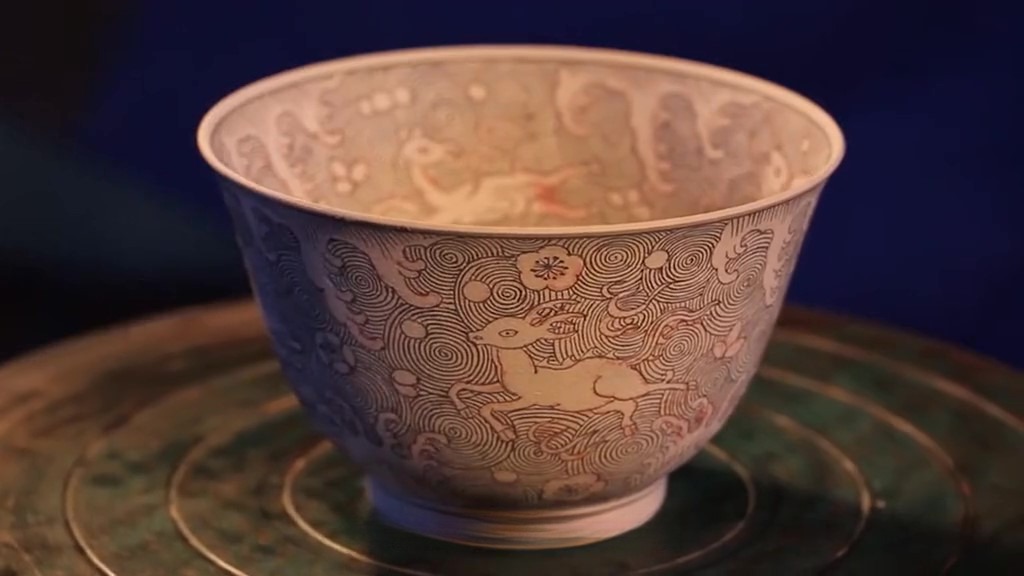
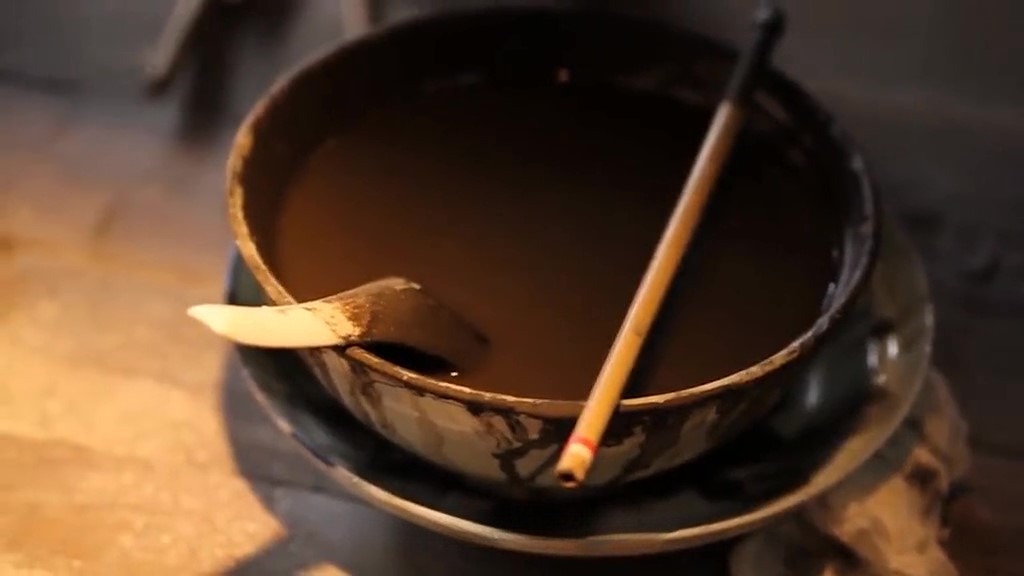
Before painting on white glaze porcelain, the various pigments are kneaded and ground in preparation. This preparation, known as “kneading the materials,” is a crucial part of the painting process. Unlike paper-based painting, the artist must consider the shape of the porcelain piece when painting.
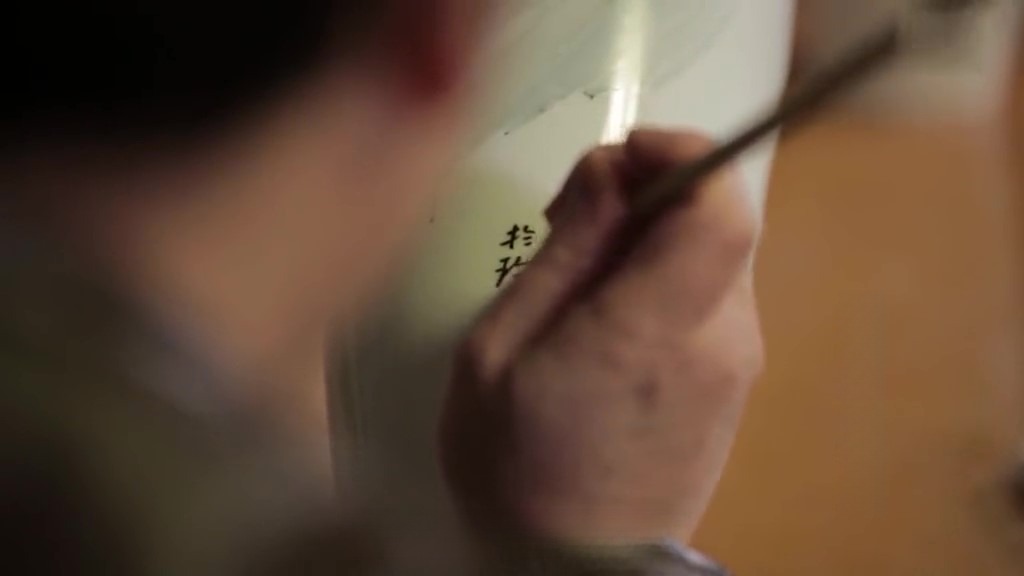
In Jingdezhen porcelain firing process, there is a detailed division of labor in the painting process, such as the distinction between oil-based and water-based blending techniques. Once the painting is complete, a person is responsible for adding inscriptions, such as the year, shop name, or poetry.
The difference between ceramic and traditional Chinese painting is that, in ceramics, the pigments used often contain mineral oxides like cobalt, iron, and copper. These pigments must undergo high-temperature firing to reveal their true colors, whereas Chinese painting pigments, made from plant materials, cannot endure high temperatures.
Handcrafted porcelain must undergo specific firing temperatures. For overglaze painting, the porcelain is fired at 800°C to bring out the color, while underglaze painting requires a higher temperature of around 1300°C to chemically alter the pigments and achieve the desired color change.
Decorative techniques such as Famille Rose, New Colors, and Ancient Colors contain lead and cannot be used on everyday porcelain because of health concerns, especially in lead-based glazes. For everyday porcelain, high-temperature glazes, such as those fired at temperatures of 1100°C to 1200°C, are preferred.
Once the porcelain is painted, it must undergo a firing process to fix the colors. This is known as “flower firing.” While ancient methods of flower firing are rarely used today, the traditional electric firing ovens are faster and more convenient. Nevertheless, the ancient method remains irreplaceable.
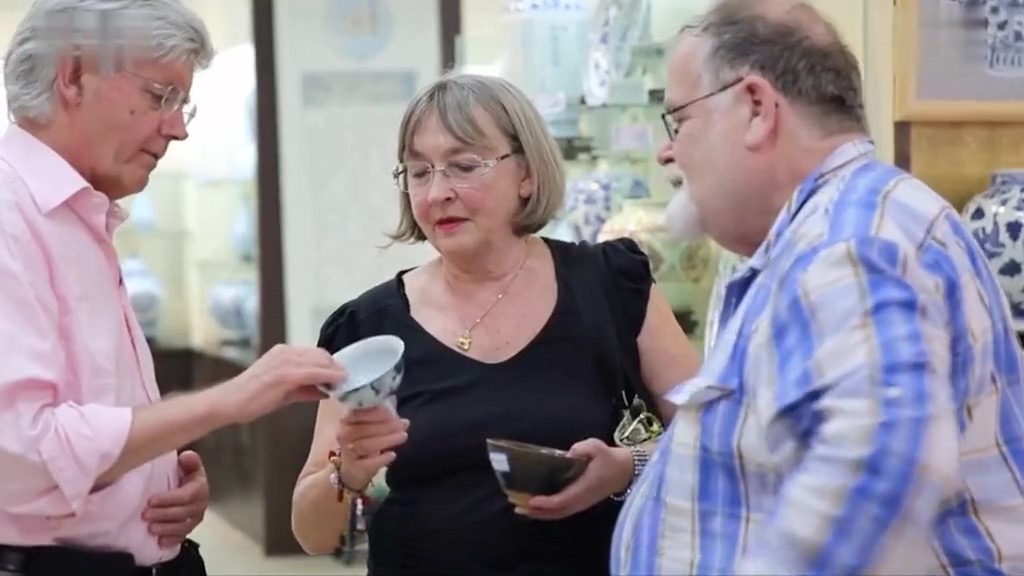
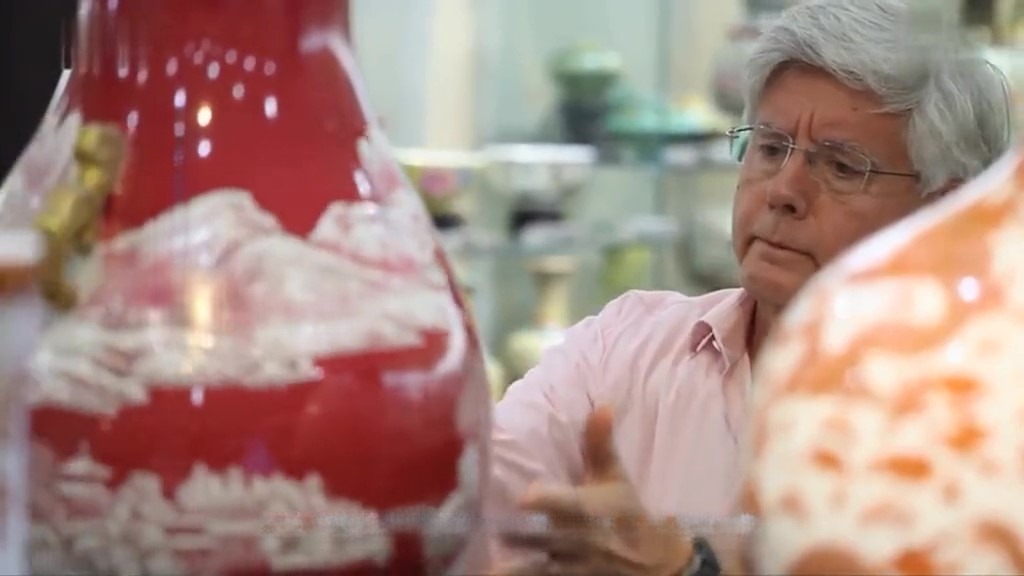
After firing, the porcelain is known as “red flower porcelain” in Jingdezhen. The quality of this porcelain is checked in a process called “color inspection,” where the employer inspects the porcelain for color consistency and quality before accepting it. The porcelain is then packaged for transport.
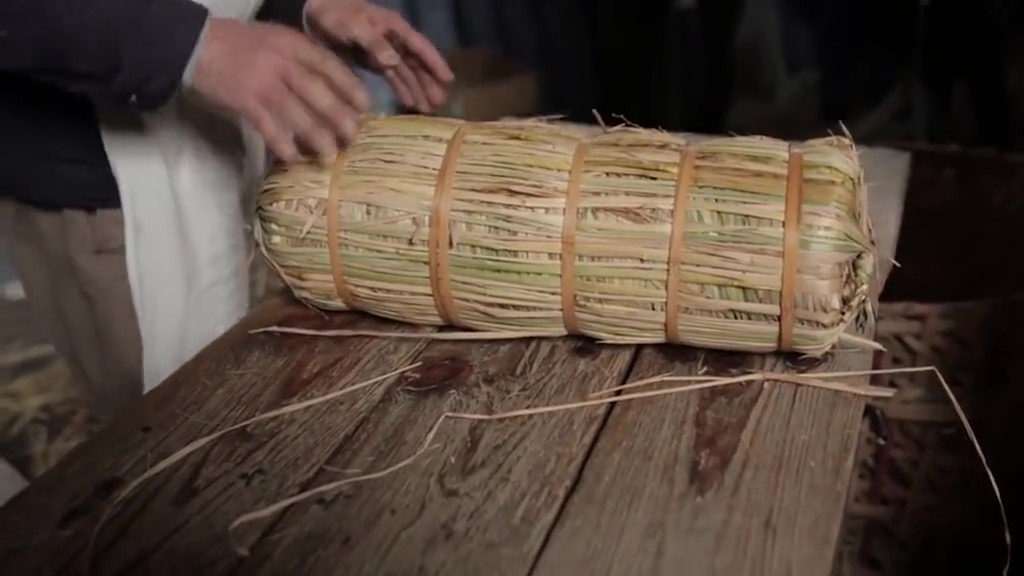
Porcelain pieces such as bowls and plates are typically packed in sets of ten, with paper padding and straw wrapping, before being placed into specially designed wooden crates for transport. However, items like bowls, cups, plates, and dishes that are not packed into barrels are bundled together in groups of thirty or fifty, bound with reed grass into cylindrical shapes. This makes transportation by both land and sea safe and convenient.
This article is dedicated to the preservation and transmission of precious traditional craftsmanship and artisanship.