How much does a handmade ceramic cup cost? Why?
In recent years, people’s demand for quality of life has been increasing. Those who value their lifestyle pay more attention to the quality of their personal belongings, as evidenced by the booming sales of handmade, hand-painted ceramic cups in recent years.
However, people seem to only notice the price of handmade cups without truly understanding what they entail. I’ve surveyed numerous forums, both professional and general, and even physical stores. The most common conclusions drawn from these inquiries are:
- Isn’t it just a ceramic cup?
- Does a handmade ceramic cup really involve such complex craftsmanship?
- Aren’t ceramic cups costing a few dollars just as usable?
- Isn’t this just marketing hype?
- I’m willing to pay for traditional, purely handmade, hand-painted ceramic cups!
- How much is your so-called purely handmade ceramic cup really worth?
In response to these conclusions, Mudan Ceramics will openly discuss the insider details of the handmade custom ceramic industry.
Isn’t it just a Handmade Hand-painted Ceramic cup?
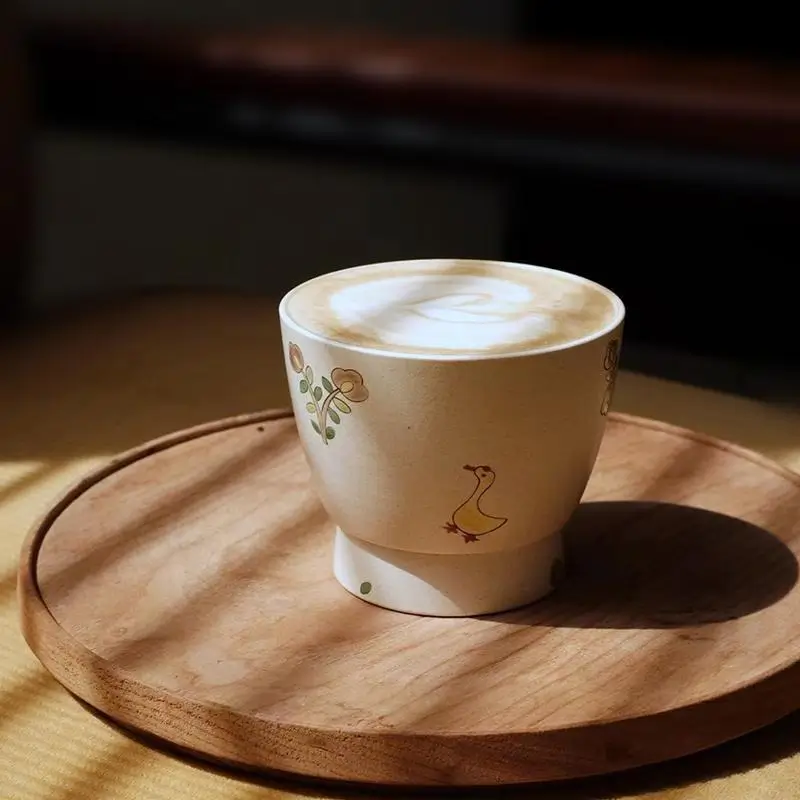
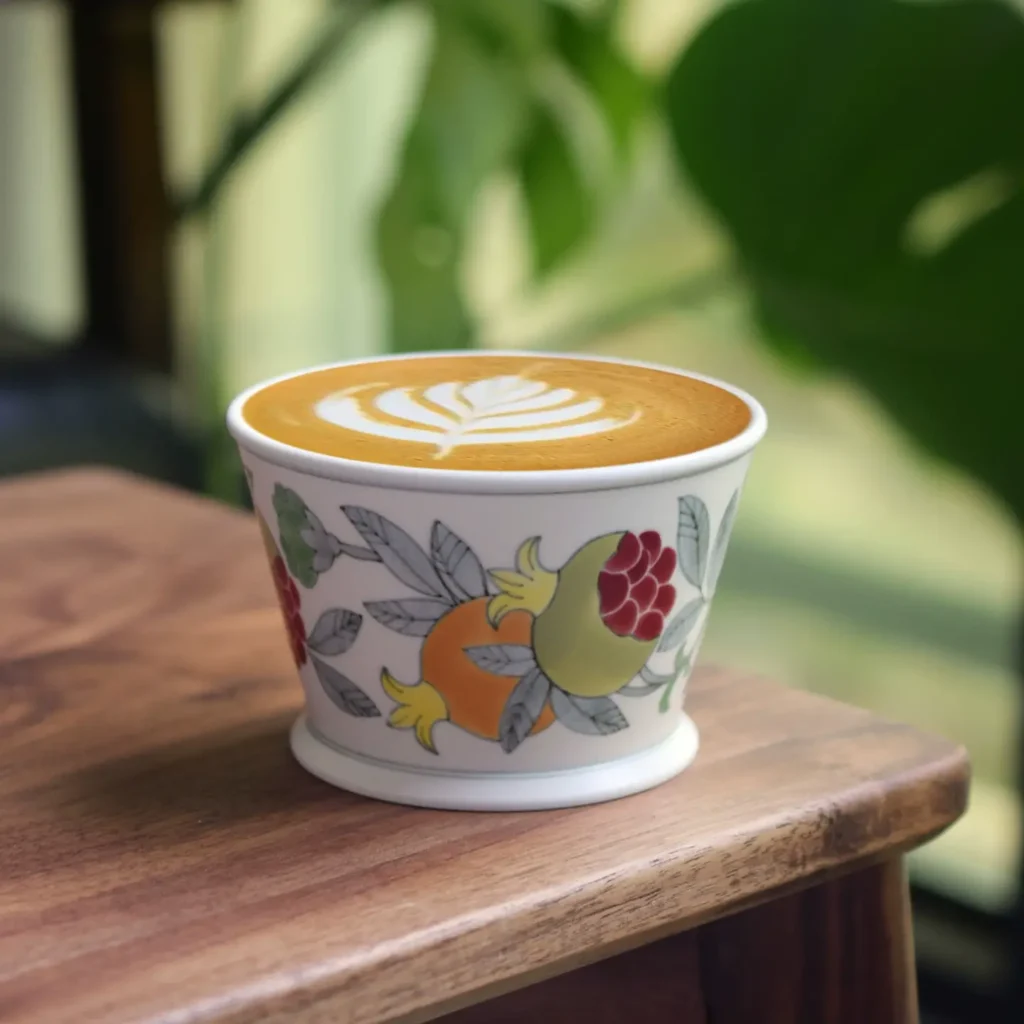
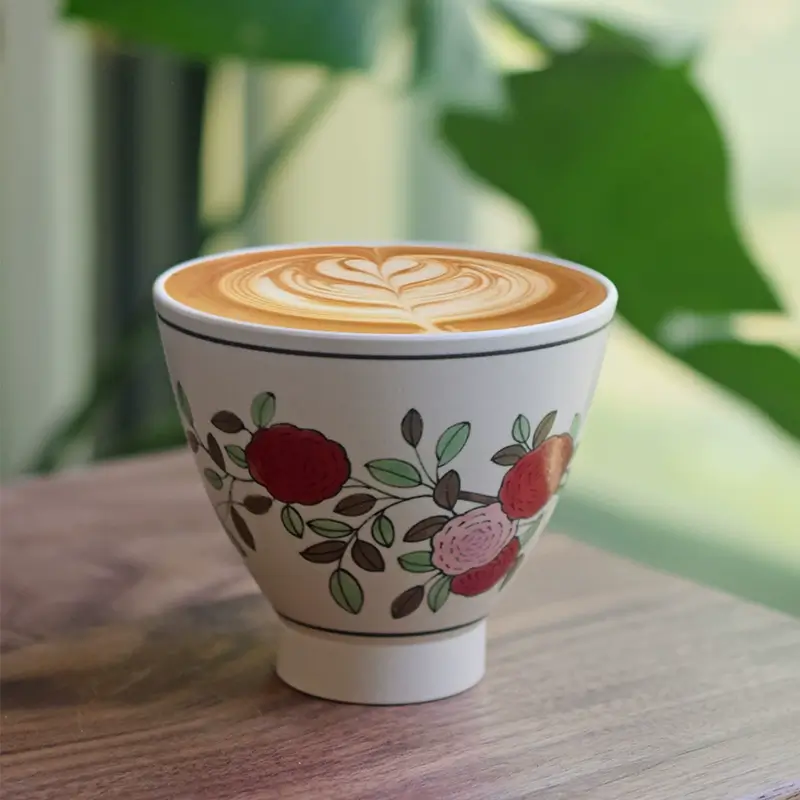
Now, let me address these questions by explaining the traditional handmade, hand-painted ceramic cups from Jingdezhen. The traditional ceramic-making process in Jingdezhen involves 72 steps. For a detailed explanation of these techniques, please refer to my previous blog posts, where I’ve done my best to present the handmade ceramic production process with both images and text.
I’ve used four articles to explain the entire process, from prospecting clay mines to packaging and shipping. After carefully reading my introduction, would you still think it’s just a ceramic cup? In a sense, it is indeed a ceramic cup, but it’s also more than just a ceramic cup!
This might sound contradictory, but after learning about the 72 steps, you’ll undoubtedly see it as a work of art. Each step is meticulous and professional, completely incomparable to modern assembly-line products made by pouring slurry into molds and machine-spraying glaze.
At the same time, you’ll feel a cultural immersion—an immersion into ceramic-making culture. It’s no longer just a piece of porcelain; it’s a vessel imbued with ceramic culture. When you drink coffee or tea from it, holding each handmade, hand-painted ceramic cup and admiring the auspicious motifs—birds, flowers, auspicious beasts, and historical allusions—you’ll unconsciously feel the weight of cultural heritage, bringing you immense spiritual joy time and time again! This is the essence of traditional handmade ceramic ware.
Does a Handmade Hand-painted Ceramic Cups really involve such complex craftsmanship?
Yes, this is the craftsmanship of traditional purely handmade ceramic cups. The 72 steps are just a summary of the major processes; delving deeper, 72 steps can’t fully encompass it! Modern processes are extremely simple: setting molds, pouring slurry, machine polishing, machine glazing, and electric kiln firing. The products are glossy and identical.
If you want a specific motif, no problem—they’ve already prepared decals to stick onto the products. In moments, a computer-engraved design is printed on. The yield rate is high, but the drawbacks are obvious: every product looks exactly the same.
Fluid artistic charm? It’s unattainable. Personalized designs? Quite unlikely. As for artistic conception, you’re simply overthinking it. Beyond being a functional vessel, there’s no spiritual pleasure to speak of. However, precisely because it’s a utilitarian object with universality, existing for civilized survival, its nature demands it must be cheap enough! It needs to solve the problem of relatively decent survival!
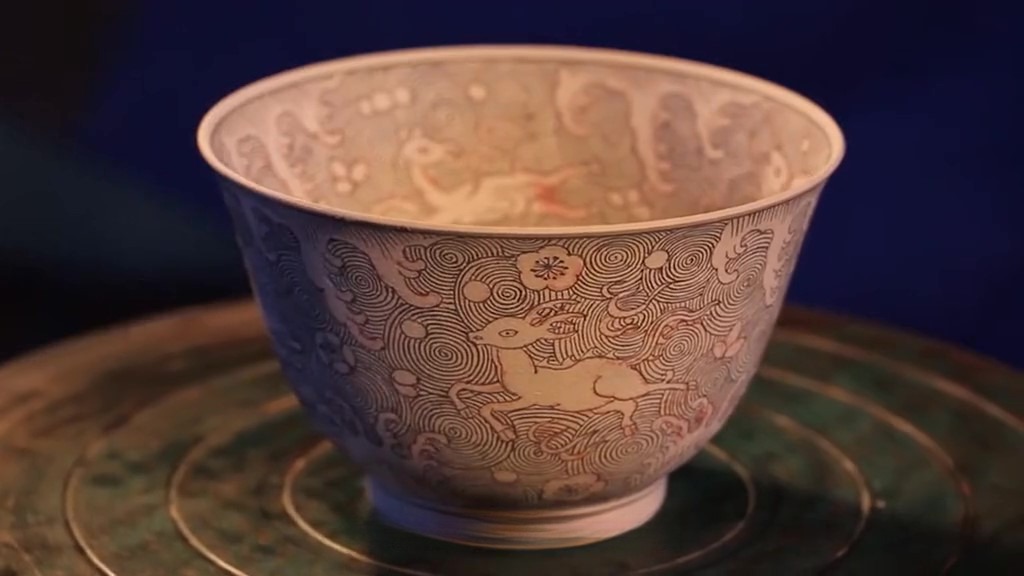
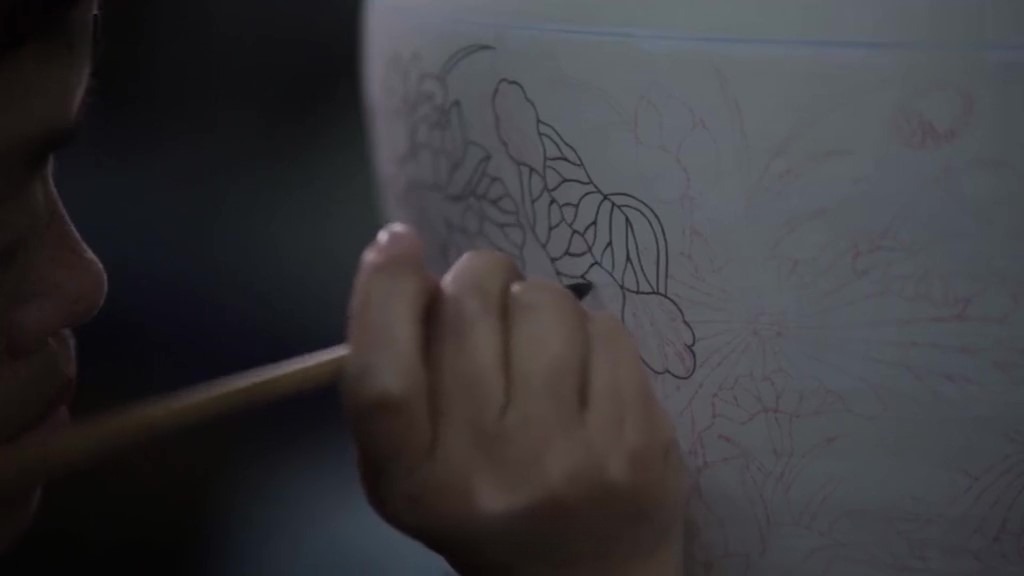

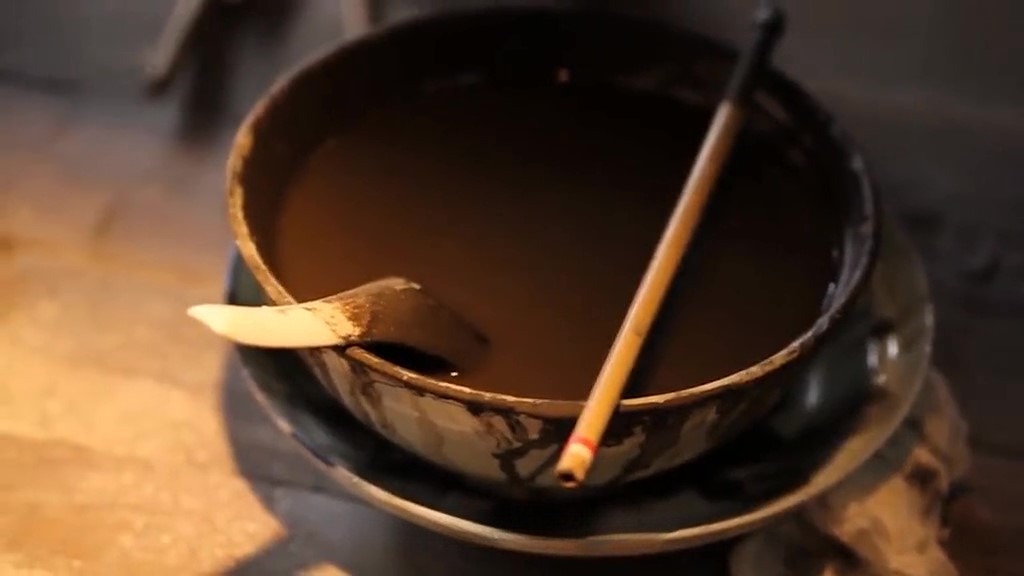
In contrast, traditional handmade ceramic cups have complex processes because each production stage carries its own significance. Why prospect clay mines? What makes setting up workshops by the river so important? How does using pinewood for firing affect the process? What’s the significance of clay from centuries-old mine pits? How does water from this specific river contribute to the final result? Specialized painters are needed for certain steps—why is that the case? And why must blue-and-white porcelain be kiln-opened only under specific weather conditions? And so on.
These aspects can’t be fully replicated by modern technology either! For example: you can computer-simulate ballistic trajectories with precision, but to solve the problem, you still need a wind tunnel. When a traditional handmade ceramic piece is finished, what you see and feel is entirely different—it’s that magical. Now, do you still think it can be simple?
Aren’t ceramic cups costing a few dollars just as usable?
This question has been answered in the first two points. Are utilitarian value and cultural (or spiritual) value the same? Moreover, even if the average skill level of production is the same, the time required is completely different! A handmade Rolls-Royce and an assembly-line car still have differences!
A ceramic cup costing a few dollars might be usable—note, I say “might”! Because I don’t know whether it’s low-temperature or high-temperature porcelain, or whether it emits a foul sulfide odor when wet. Here’s my advice: for tableware used daily, always choose branded products if possible. If absolutely necessary, opt for higher-priced items under the same visual conditions, and avoid overly vibrant colors. White is best, or high-temperature (1300°C) ceramics like ours!
Isn’t this just marketing hype?
Impossible! The reason traditional handmade custom ceramics have been passed down for millennia, growing more vibrant with time, is because they embody a robust culture! That’s why they’re so enduring—marketing can’t fabricate this. Even if we’re talking about marketing, the famous 4P marketing theory lists “product” as its first principle. Why is it the first? The answer is obvious: because all subsequent marketing activities are based on the product! Without a strong product, the rest is moot!
I’m willing to pay for traditional purely handmade, hand-painted ceramic cups!
You’re not just paying for a traditional handmade, hand-painted ceramic cup—you’re paying for ceramic culture! You’re paying for that cultural spirit. Since ancient times, literati and artists have used pottery as a medium to create countless motifs for cups, each rich with profound meaning and symbolism, leaving people endlessly fascinated and deepening their spiritual world over time.
How could you not love such a culture embodied in porcelain? You’re not buying a cold, lifeless vessel—you’re buying a culture that refines your temperament! I, too, am willing to pay for this!
How much is your purely handmade ceramic cup really worth?
Here, I’ll use Mudan Ceramics as an example to provide a report: Our four artists at Mudan Ceramics work on four distinct series, each with its own characteristics. Take ZHIGU, for instance—it’s a classic example of traditional handmade, hand-painted porcelain. The clay is sourced from time-honored, meticulously refined mines. To fully express his creative vision, the artist personally throws the坯 (clay body) based on the motif’s characteristics, rather than using pre-made坯. This process takes about 2 hours, and since there’s a yield rate, multiple坯 are made at once. Trimming the坯 also takes time—this isn’t a secret, so I’ll tell you: an average of 45 minutes.
Next comes hand-painting based on the drafted motif. Simpler patterns take less time—but “simpler” here refers to the motif’s complexity, not the number of杯体 (cup bodies). Even so, many assume single-branch flowers are simple, which is a mistake. In reality, seemingly simple motifs are often the most challenging—with fewer reference points, the means of expression are limited. To achieve fluid charm and avoid stiffness, solid foundational skills are essential! This hand-painting process takes about 2–5 hours. With inspiration and good手感 (hand feel), the average is still 2.5 hours.
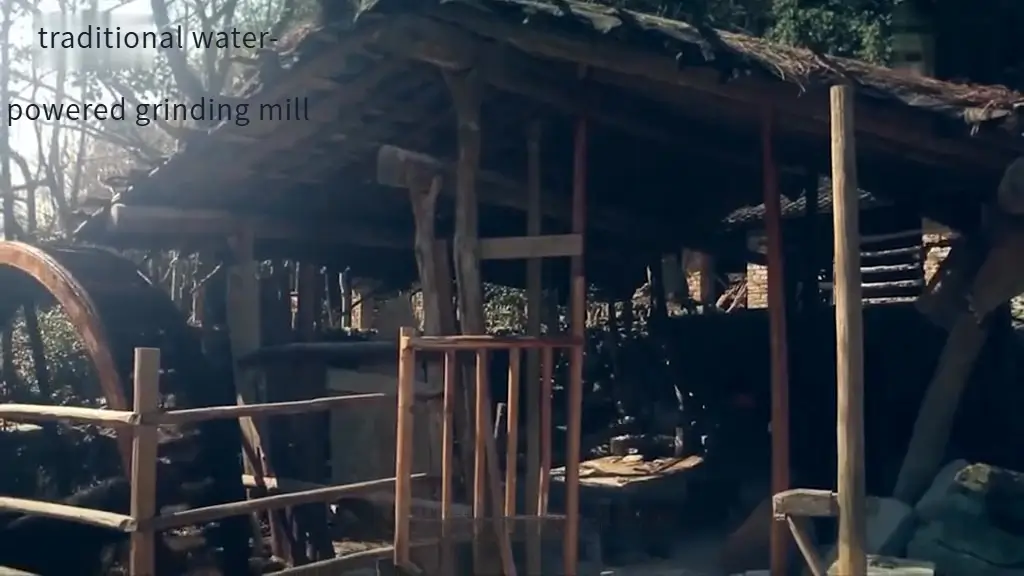
Firing time is considered universal here, as Mudan Ceramics uses one of Jingdezhen’s top ten kilns, so we won’t factor that in. Thus, a single traditional handmade ceramic cup requires over 5 hours of labor.
Our young artists don’t have high output. Even without considering溢价 (premiums), if we calculate based on average labor time at $30 per hour (reasonable, right?), you can do the math on the cost. Fortunately, with the internet and modern planning tools, our artists can focus on creation, improving efficiency. Even so, production can’t keep up. But Mudan Ceramics won’t expand or alter this process for commercial reasons.
Once again, Mudan Ceramics must clarify: our inventory is very limited. If you wish to purchase more than 5 pieces, please contact us first so we can better serve you and provide a suitable solution.