The Craft of Perfection: A Deep Dive into the 72-Step Handmade Porcelain Process (Part 1)
Today, I’m taking you behind the scenes of traditional handmade porcelain to show how a raw stone transforms into a beautiful piece of ceramic art through skilled craftsmanship.
Handmade porcelain process —Mining and Processing the Porcelain Stone
The journey of handmade porcelain begins with the mining of porcelain stone. The stone undergoes processing, crushing, washing, and repeated sedimentation to yield high-quality, fine porcelain clay. The clay is then kneaded and worked hundreds of times to ensure it’s uniform and delicate enough to meet the stringent requirements for porcelain making.
Wheel Throwing and Trimming — The Test of Skill
At this stage, the artisan’s craftsmanship is tested. Precise control over the wheel speed and pressure is essential, as even the slightest error could ruin the piece and require starting over. The trimming process demands close attention to detail, ensuring every curve and line is perfectly symmetrical. True artisans often dedicate their lives to mastering one or two designs, striving to achieve perfection within a narrow focus. For instance, some artisans specialize in blue-and-white porcelain, creating only a few timeless pieces throughout their careers.
Handmade porcelain process — Making and Applying Glaze
The quality of the materials, the skill of the artisans, and the quality of the glaze are all foundational to success. However, the glaze formula is a closely guarded family secret, passed down through generations and kept private. For example, descendants of the Ming and Qing Imperial Kiln artisans in Jingdezhen, or the Longquan Zhang family’s celadon, continue to protect their recipes through word of mouth, ensuring that no written records leak.
Modern technologies have gradually uncovered these traditional formulas. Generally speaking, glazes follow the SiO₂-Al₂O₃-RO/R₂O chemical system. By adjusting the ratios of different ingredients, we now enjoy the vibrant world of handmade ceramics.
Basic glaze: SiO₂ (60-75%) + Al₂O₃ (8-15%) + Flux (10-25%)
Colorants: Fe₂O₃ (for celadon) / CuO (for red porcelain) / Co₃O₄ (for blue-and-white porcelain)
Special additives: Bone ash (milky glaze), plant ash (iron-based crystalline glaze)
The glaze-making process involves grinding, filtering, and mixing. Applying the glaze requires finesse—whether dipping, pouring, or spraying, each method demands perfect execution. The thickness of the glaze and the control over its flow are essential to achieve the desired effect. Since glazing is a one-time process, every layer applied is a step towards achieving the ideal porcelain aesthetics.
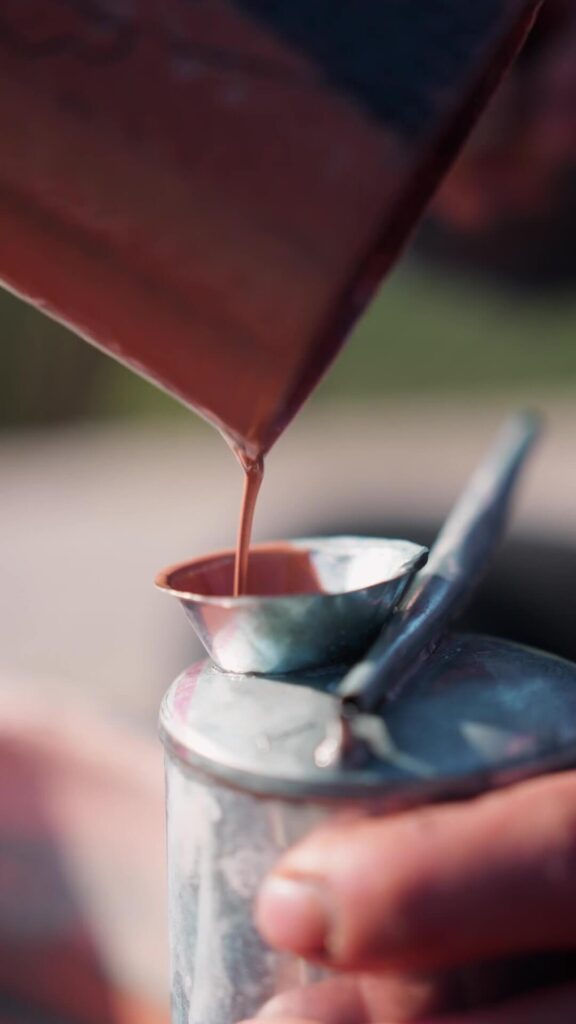
Painting and Decoration — The Artisan’s Touch
The painting and decoration of porcelain require the artisan to be highly focused, with every stroke needing to be precise. Techniques such as blue-and-white, famille rose, and underglaze red have been passed down through millennia, requiring absolute precision. The intricate details in the hand-painting often define the soul of the piece. For example, blue-and-white porcelain requires special cobalt blue pigments, and the design must be flawlessly drawn on the glazed surface. Even the tiniest detail must be perfectly executed. This technique not only challenges the artist’s talent but also their skill and patience.
Firing and Shaping — The Rebirth of Clay
Finally, the kiln loading process must be handled with care. Firing temperature control is critical—an error of a single degree can affect the final quality. Jingdezhen’s ceramic masters rely on their extensive experience, often judging the kiln temperature by observing the color of the flame and feeling the heat. For example, by observing the flame’s color shift (from sodium yellow to potassium purple), they can judge temperature changes, with an error margin typically under 10°C. This type of experiential knowledge often surpasses the accuracy of instruments.
In certain ceramic works, such as the “Yao Bian” effect in Jian ware, precise temperature control is essential. Achieving this effect requires firing at 1230°C ±5°C, with rapid cooling—a process entirely dependent on experience rather than instrument measurement.
Jingdezhen’s traditional wood-fired kiln masters, known as “Ba Zhuang,” take this expertise to the extreme, ensuring that every firing is executed to perfection by observing even the slightest changes in the flame color, ensuring the ideal conditions for firing each piece.
The quality and appearance of fired ceramics depend not only on the precision of each step but also on the artisan’s unique understanding of the piece and their pursuit of beauty. It’s these finely honed details that turn each porcelain piece into a one-of-a-kind masterpiece, imbued with exceptional vitality.
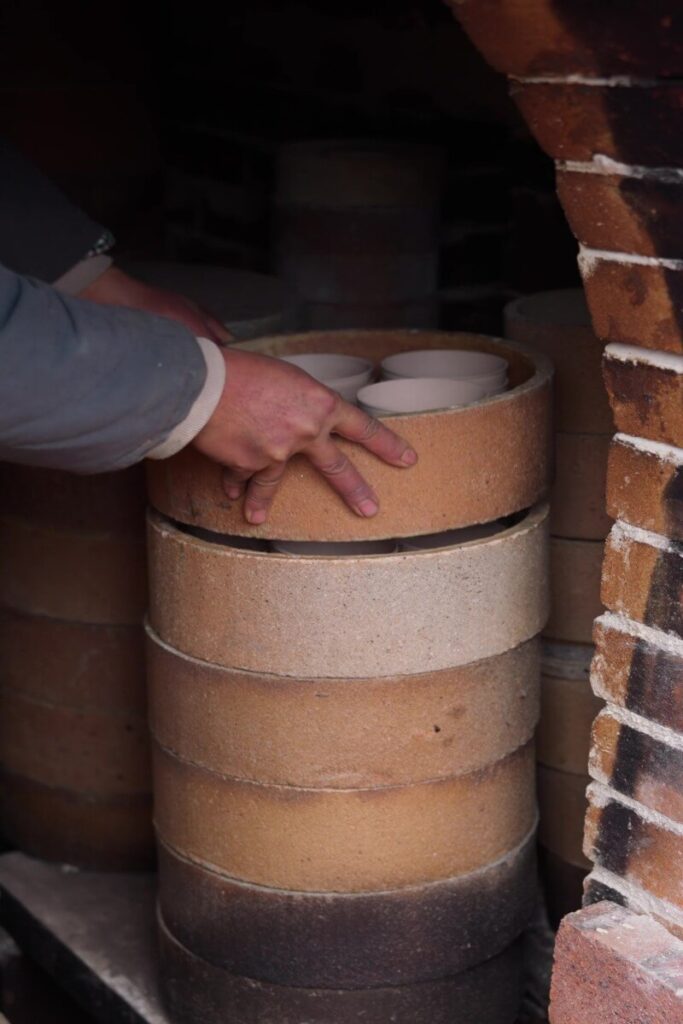
The Combination of Art and Practicality
Handmade ceramics are not just artistic displays—they are companions in daily life. Whether used as coffee cups or decorative plates, each piece reflects the artist’s love for life and their dedication to aesthetics. Many handmade porcelain works have both artistic value and practical function, fitting seamlessly into modern home life. Every piece can find its place in daily life, becoming the highlight of a home’s décor.
Stay tuned for the next chapter of this visual journey, where we will continue to explore the fascinating world of traditional handmade porcelain!
Supplement: Detailed Process of Handmade Porcelain Production
Following the previous introduction, here is a detailed description of the mining, material preparation, forming, glazing, painting, and firing processes involved in traditional handmade porcelain craftsmanship.
Handmade porcelain process-Mining and Processing of Porcelain Stone
Mining: Open-pit Mining in Quarry
Processing:
- Stone Crushing: Crush porcelain stones into egg-sized pieces
- Grinding: Pulverize into powder using a water mill
- Washing: Stir and wash in washing pools
- Sieving: Precipitate and separate, discarding coarse particles
- Pulping: Transfer the slurry into thickening pools to condense into clay pulp
Mining and Processing of Kaolin
Mining:
Open-pit or Shaft Mining in Quarry
Processing:
- Stone Crushing: Crush porcelain stones into egg-sized pieces
- Grinding: Pulverize into powder using a water mill
- Washing: Stir and wash in washing pools
- Sieving: Precipitate and separate, discarding coarse particles
- Pulping: Transfer the slurry into thickening pools to condense into clay pulp
Handmade Porcelain Body Production
Clay Preparation
- Test Firing: Determine the proportion of porcelain stone and kaolin
- Batching: Quantify and mix the slurry according to the proportion
- Slurry Mixing and Washing
- Thickening: Adjust slurry moisture to a hand-kneading consistency
- Aging: Let the clay age for 1-3 months to enhance plasticity
- Clay Wedging: Step and knead the clay to improve density and uniformity
Forming the Body
- Kneading: Remove air bubbles and balance moisture in the clay
- Throwing: Shape the body on the wheel
- Trimming: Refine thickness and surface smoothness
- Drying: Naturally air-dry to prevent deformation
Handmade porcelain process-Glaze Production and Application
Glaze Production
- Glaze Ash Preparation: Burn slaked lime and fern plants together
Glaze Mixing
- Mix ceramic glaze slurry with glaze ash
- Top-grade glaze: ten parts clay to one part ash
- Mid-grade glaze: seven to eight parts clay, two to three parts ash
Glazing Methods
- Internal Glazing: Apply glaze to the interior surface
- Spray Glazing: Spray glaze onto the outer surface of large wares
- Dipping Glaze: Dip daily-use ceramics for external glazing
Handmade Blue-and-White Pigment Processing
- Calcination: Fire at lower residual heat areas in the kiln
- Selection: Grade pigments based on size and quality
- Grinding: Grind the pigments with water in crucibles until fine
Handmade porcelain process-Painting
Painting Tools
- Goat-hair brushes, blue-and-white painting brushes (outlining brushes), Fen Shui brushes, etc.
Painting Techniques
- Sketching: Design and outline patterns on the body
- Outlining: Trace and define pattern lines
- Fen Shui Techniques: Including flat coloring, shading, blending, overlaying, and splashing techniques
Handmade porcelain process-Firing Process
- Loading: Place handmade ceramics into appropriate saggars by size
- Sealing: Seal the kiln mouth
- Firing: Fire with pine wood for 24+ hours
- Unloading: Cool down and then remove the porcelain